By Nathaniel Luce
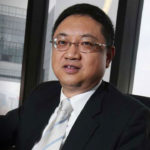
Austin Na (MBA’95)
Across the world, Vanderbilt Business alumni find themselves on different frontlines of the COVID-19 pandemic. In the first installment of COVID-19 Insights, Austin Na (MBA’95) shares his thoughts on the state of supply chains and what he’s learned as a business leader in these challenging times. Austin Na is the Chairman and CEO of O-Net Technologies, a manufacturer of optical networking products and machine vision systems and sensors.
How has the global pandemic broadly impacted manufacturing supply chains?
I believe the global pandemic has seriously impacted manufacturing supply chains. Many industries are experiencing shortages of supply due to the shut-downs of supplier factories around the globe. Some suppliers, despite continuing operations, are only at partially normal production levels due to a lack of sufficient operators. In recent months, the situation has become more and more worrying, as the pandemic is still developing in many countries.
Are certain sectors of manufacturing more impacted than others? If so, how?
Yes. The sectors that are impacted the most are the ones that supply the industries that are hit the hardest, such as tourism, airline and travel, outdoor dining and entertainment, etc. On the other hand, sectors that people are using more during the lock-down are booming. Telecom equipment is a good example. Many companies in this sector are experiencing higher-than-expected demand due to sudden rise of purchase orders from internet service operators.
What can manufacturers with global operations do to mitigate supply chain disruptions?
This difficult time is obviously a test of the supply chain management capabilities of multinationals. To improve delivery and avoid supply chain disruption, companies are required to do a better job in forecasting and planning. Closer communications with key customers is becoming critical. In some cases, companies have to increase their buffer stocks beyond normal levels to cope with supply chain shortages.
What have you learned about your own operations as the pandemic spread across the globe, and how do you apply those learnings to business operations?
Our global operations experienced all of the development phases of this pandemic around the globe. Our manufacturing headquarters in Shenzhen, China was forced to shut down during February. After the Shenzhen factory resumed operations in March, our factories in France and Canada had to close down for two weeks following a government order. Currently, our French and Canadian facilities are in partial operation.
We did learn a lot through this experience, such as how to keep a disciplined team, how to set up solid protective rules and regulations, how to act fast and in-time, and how to keep customer commitment while keeping our team safe and healthy. We will benefit from such experiences for years to come.